Fiberglass Repairs
request your quote now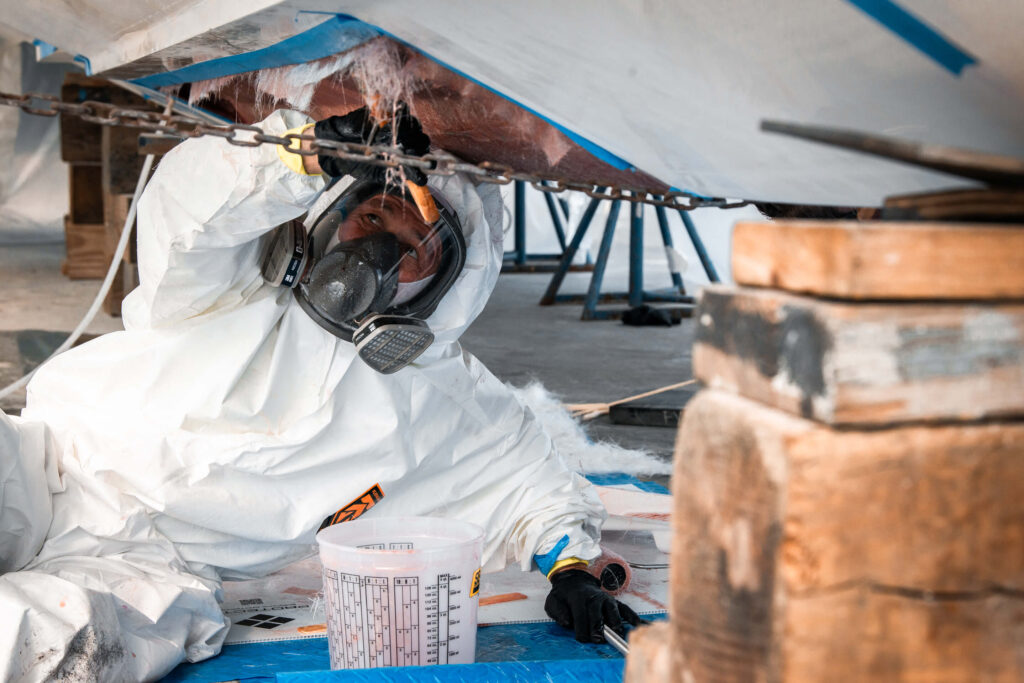
Expert Fiberglass Boat Repairs
At Foster’s Yacht Services, we excel in fiberglass boat repair and painting, adhering to the highest standards. Our meticulous approach ensures that no shortcuts are taken, delivering superior results.
The Precise Repair Process:
- Grinding: Utilizing a 5” or 7” grinder, we assess the size and depth of the damaged area. Any delamination, cracks, voids, blisters, spalls, or detached plies of fiberglass laminates are thoroughly ground out.
- Beveling: We bevel and feather the edges of the ground-out areas with a 3 to 1 taper width to depth ratio, ensuring a seamless transition with the surrounding intact fiberglass.
- Preparation: Before laminating, the area is wiped clean with acetone to remove any residue. The appropriate fiberglass material, such as ¾ or 1 ½ ounce CSM, 1708 or 1808 stitched Biaxel, or a heavier 24-ounce cloth like Rovimat, is cut and measured.
- Laminating: Using catalyzed Vinylester or Epoxy resin, we meticulously lay patches of fiberglass laminates matching the dimensions and shape of the prepped areas. Multiple ply groups are added to achieve a flush surface with the surrounding intact fiberglass.
- Tapered Laminate: Each successive fiberglass ply group is cut 2” larger than the last ply group to create a tapered laminate step back for structural integrity.
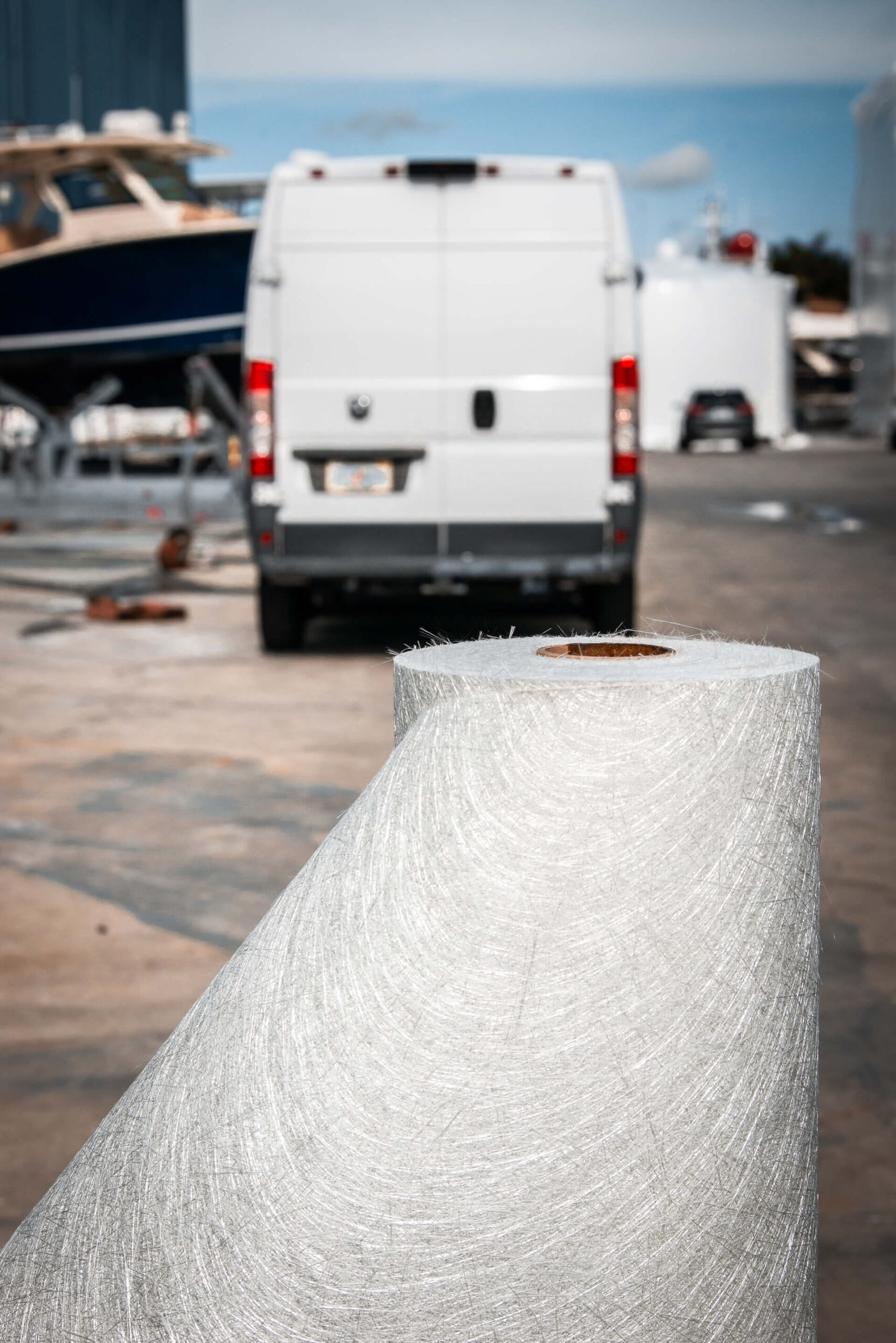
- Surface Finishing: A final layer of 1 ½ ounce (CSM) or chopped strand matt ensures a smooth and even surface. Excessive exotherm is avoided during the laminating process, not exceeding 122 degrees Fahrenheit or 50 degrees Celsius.
- Polishing: After proper sanding, the area is polished using a marine-soluble compound like Aqua Buff 2000 or Profile 500, followed by Imperial finishing Compound and/or glaze. A marine-grade UV wax can also be applied for extra protection, with recommended intervals for reapplication.
- Final Surface: Fillers are applied, not exceeding a ¼ inch in depth, and sanded uniformly until the area is even and fair. For Gel coat final sanding, finer grit sandpaper is used.
- Priming and Coating: The surface is prepped, masked, and sprayed with 2-part epoxy primer or color-matched polyester catalyzed gel coat. Additives like liquid wax solution or Duratec Products prevent post-curing tackiness.
- WHAT OUR CUSTOMERs SAY ABOUT US
TESTIMONIALS
EXCELLENT Based on 20 reviews Phillip Pyatt2023-08-11 These guys do very good work. They repaired some fiber glass and an anchor plate along with adding a coat of paint to the hull. Yacht Pro USA2022-12-23 We have used Fosters for years and its definitely the best company out there for fiberglass, paint and refits. Dennis is always professional and we highly recommend them for any needs in our yacht industry. John Marshall2022-11-21 Fosters Yacht Service is my preferred company to use for yard maintenance while in Ft. Lauderdale. Dennis, Erick, and Mark know the industry and how to get things done. Fosters keeps to their word and deadline. Highly recommended. Evan Davis2022-10-11 We started with Foster’s to repair some structural hull issues. They exceeded expectations with the repairs. We also had them do multiple repairs throughout the vessel from exterior paint to interior carpentry. The fit and finish have been amazing. scott adams2022-09-21 As a marine industy professional it has been my direct experience to have this Group (Foster's Y/S) care for and upgrade my families Hardin 45 ketch. Everyone at Foster is a team member at Your disposal if required. We have found that Foster's high quality work in conjunction with Great customer service are the foundations found here. "Trade Winds" will be back next year for some further upgrades. Thank You for helping us sail away... Russell Gross2022-08-19 Dennis Foster and his shop are amazing. My boat had extensive fiberglass damage which was made worse by another repair shop. Dennis came to the rescue. Boat came back brand new and faster than promised. If you need any fiberglass work done, don’t go anywhere else! Thank you Dennis and team! David Torchin2021-10-19 I brought my 2018 Formula to Dennis Foster to make my arch collapsible and make the boat able to sneak under low bridges by my house. Dennis and his team way exceeded my expectations!!! With the press of a button, my bridge clearance is now just over 6'. His work is flawless, and his team is friendly and professional. Thank you Dennis and team for the amazing results!!